智能制造工业4.0与供应链之间的协同作用(二)
自主框架计算机系统应用于装配制造之日起,材料需求计划(MRP)功能一直支持制造过程,既可以作为独立的“引擎”,也可以作为更广泛的企业的组成部分。资源规划(ERP)解决方案。MRP的目的非常简单:为材料下订单,使其具有足够的准备时间,以便材料及时到达工厂以满足其消耗要求。即使在今天,随着MRP和ERP功能跟随计算趋势并开始迁移到云中,一个基本问题是,这些仍然是在当今现代工业4.0驱动的工厂中使用的正确工具,或者这些是否需要发展,加强,甚至更换,以满足更极端的操作灵活性要求,以及应对市场上不稳定的材料可用性。当然,似乎没有帮助,它们的相关性正在下降。作为数字工厂的一部分引入的新工具的集成是否可能成为MRP和ERP的新生命?
MRP在现代工厂中独立工作的能力
对于许多人来说,必须处理材料短缺和供应问题的挫败感始于MRP明显未能达到目标。公平地说,MRP预期工作的环境近来发生了显着变化。要了解最近变化的影响,可以检查使MRP有效运作所需的三个关键因素:
- 有关生产什么产品以及何时生产的信息
- 可见工厂已有的材料
- 了解材料使用的灵活性
有关产品的生产和数量的信息主要来自ERP流程。ERP的传统方法是查看长期销售预测,并从中创建满足此类需求的工厂计划,确保工厂和客户之间产品分销链中的每个节点都得到充分保持。随时放养。ERP计算是严格的,但往往反映销售组织的主观数据,因为它们预测每种产品的可能销售。当产品的生命周期相对较长时,大多数产品将体验到稳定的客户需求,这些需求可以通过营销促销轻松引导和影响。生命周期中要求更高的领域是新产品推出,需要在整个分销链中建立新产品的库存,基于对潜在需求的预期,以及产品的寿命终止,产品的库存需要在不需要的情况下“冲洗”过度贴现。由于长期稳定的需求,工厂认为预测和实际交付要求之间的差异很小,主要关注的是质量问题,因为它代表了按时交付的最主要威胁。
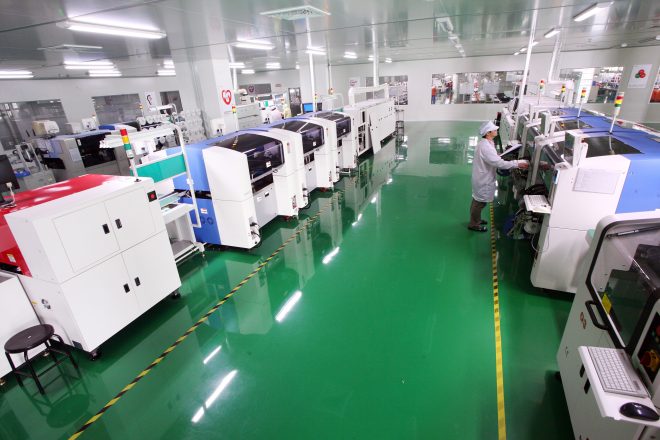
然而,对于大多数装配制造领域而言,制造具有长寿命周期的产品的这种条件代表了制造业的“黄金时代”,由于电子市场中竞争的全球性质开始侵蚀利润,因此现在几乎消失了。随着技术发展的加速,需要更快,更频繁地以更低的成本将新的和更多样化的产品引入市场以应对竞争。分销链被立即确定为此活动的主要威胁,因为在许多情况下与产品分配相关的成本超过了实际制造成本。通过在配送链中拥有大量成品以及相关的存储和物流成本来实现纯粹的投资是一种简单但不舒服的计算。
此外,随着越来越多的产品和变体进入市场,产品生命周期显着减少。新产品引入和寿命终止之间的稳态需求期迅速减少,并且在某些情况下完全消失,导致需求波动程度更高。然后,分销链中股票价格下降的成本对整个业务来说变得非常重要。这种趋势的影响是大幅减少整个分销链中的成品数量,使其尽可能精益。对于工厂来说,这已经变得越来越重要,因为在分销链中缓冲库存减少,市场需求的波动性对工厂计划产生直接影响,在需要较小批量的产品数量方面,导致产品组合逐步增加。这对工厂生产率的影响反过来显着,对于挥发性短生命周期产品,长生命周期产品的连续生产通常可达到80%或更高,大幅降低到20-40%甚至更低。因此,大规模生产导向的ERP和MRP受到挑战,这仅仅是因为他们意识到分销链中的成本会导致任何长期承诺的减少。对于挥发性短生命周期产品,对于持续生产的长寿命产品,通常可实现的总生产率水平为80%或更高,被削减至20-40%甚至更低。因此,大规模生产导向的ERP和MRP受到挑战,这仅仅是因为他们意识到分销链中的成本会导致任何长期承诺的减少。对于挥发性短生命周期产品,对于持续生产的长寿命产品,通常可实现的总生产率水平为80%或更高,被削减至20-40%甚至更低。因此,大规模生产导向的ERP和MRP受到挑战,这仅仅是因为他们意识到分销链中的成本会导致任何长期承诺的减少。
这一趋势现在已经到位,触发了工业4.0的创建,工业4.0认识到需要采用全新的方法来实现制造,以满足短期的产品生命周期和客户需求模式的变化。工业4.0支持客户需求与工厂供应的紧密结合,许多人认为这有利于靠近客户的生产运营。这对于近年来普遍存在的本土低成本远程制造模型来说是不利的。工业4.0已被视为扭转偏远制造趋势,在主要西方国家创造制造业就业和经济价值的途径。这种潜力为制造业企业领导者改变工业4.0创造了强大的动力,无论采取何种形式。在工厂和客户之间几乎没有缓冲库存,并且在许多情况下直接运输,实现了管理人员工业4.0工厂需要像“按订单生产”一样运行,但当然,“批量生产”效率”。这种情况超出了传统ERP的范围。
MRP的下一个挑战是了解工厂中存在的材料。应始终将这些材料中的每一种都计入并分配给各种先前计划的产品和工作订单。然而,越来越多的是出现“内部”材料短缺,即ERP期望材料可用的情况,但事实上,它们无法在物理上定位。这种情况引发的直接行动是增加工厂可用的材料数量,以确保始终有足够的材料,以免导致生产执行停止,从而影响产品的交付给客户。然而,这种材料膨胀只会延迟内部短缺的发生。
由于内部短缺继续发生,分配给其他工作订单的材料通常会被“窃取”以保持生产线运行,这只会导致其他地区的生产不足。在许多情况下,采取了极端措施,以确保仓库和车间的材料不会被误用,并建立网箱和安全检查站。最终,需要以完整库存计数的形式重置内部物料流程。这需要定期进行,具体取决于问题的严重程度以及所需的其他材料的投资限制或可用性。在大多数情况下,完整的库存需要两到三天才能完成,每个计数的成本代表工厂总生产力损失1%。在实践中,每年必须进行一次或两次库存计数。由此产生的数据显示,ERP所拥有的材料已经被移动到或位于车间,因此显然缺乏可见性。
例如,一个相当大的装配制造业务经常发现他们有100万美元的股票在ERP中列出,但它实际上并没有出现在工厂,但与此同时,在该工厂发现了价值300,000美元的过时库存。 ERP没有记录的工厂。问题的根源在于ERP将材料以“推动”材料的形式分配给生产,作为材料包。
套件通常包括完成每个工作订单所需的所有材料,无论是每台机器还是整条生产线。SMT材料的性质是它们以散装卷轴或其他载体供应,每个载体上有1,000到10,000个零件。这些供应形式是由于元件尺寸小,大批量生产所需的大量以及SMT贴片机的运行速度而产生的。当考虑较小的批量时,很可能几乎每个套件中的每种材料都会产生,所供应的材料数量将大大超过所需的数量。典型的批量可以是200件产品,每件产品只需要一件材料,来自卷轴,其中有数千件过量供应。另外一个问题,当卷轴设置在馈线上或从馈线上移除时,会丢失一定数量的材料。在机器运行期间发生额外的材料腐蚀,特别是在制造初始产品时。结果是,当工作单执行时,实际消耗了超过所需数量的未知数量的材料。工作结束时的材料卷轴留下了未知数量的材料。计算剩余材料是耗时且侵入性的过程,需要大量的材料处理,这可能损坏材料和包装。结果是,当工作单执行时,实际消耗了超过所需数量的未知数量的材料。工作结束时的材料卷轴留下了未知数量的材料。计算剩余材料是耗时且侵入性的过程,需要大量的材料处理,这可能损坏材料和包装。结果是,当工作单执行时,实际消耗了超过所需数量的未知数量的材料。工作结束时的材料卷轴留下了未知数量的材料。计算剩余材料是耗时且侵入性的过程,需要大量的材料处理,这可能损坏材料和包装。
通常情况下,计数实际上并没有完成,即使是这样,也很少有时间手动更新每个材料的实际使用量。机器操作员的优先事项是使用下一个材料套件使机器在下一个工作单上运行。其结果是,在车间看不到数量未知的非托管材料的存储量增加,而ERP则无法存储。这个问题的严重程度随着批量的减少而扩大。然而,在生产线附近本地保存的材料的明显可用性是生产操作接受甚至鼓励,因为这加速了它们应对套件中意外材料短缺的能力。然而,事实是腐败,损失,对材料的破坏不可避免地导致ERP记录与物理世界之间库存水平的不匹配增加,以及影响质量。对于无法看到的损失,MRP根本不会订购替换材料。
MRP的第三个挑战与制造过程的灵活程度有关,包括何时需要材料以及可以采用何种替代方案。物料清单(BOM)信息源自产品设计。将设计数据传输到SMT制造的最常用的方法是以PCB图像的图形的形式,格式称为Gerber,最初基于HP绘图仪绘图标准,以及许多其他图表,图片和有关组件位置,电气节点等信息的列表。装配过程工程团队必须获取这些文档并创建产品模型,以便他们为每台机器创建详细的过程说明和信息,并将手动操作用作装配和测试过程的一部分。
由于这个漫长而复杂的程序,在将更多新产品引入工厂的时候,工程团队必须事先决定使用哪种生产线配置来生产产品。然后,很少有机会更改配置,甚至更改要使用的实际材料,这可能需要不同的机器配置和程序设置,具体取决于其供应格式和物理属性。结果是,产品将有效地在专用生产线上运行,生产率保持不变 – 并且根本不符合实际的客户完成或交付要求 – 并且将使用严格控制的一组材料。
由于MRP背后的三个主要驱动因素受到行业趋势的影响,因此今天工业4.0制造业的MRP,甚至ERP的前景看起来非常暗淡。由于生产需求正在不断变化,MRP并不清楚何时会生产什么产品或什么时候生产。MRP无法查看工厂中实际的材料数量,也不知道它们的位置和分配方式。在选择每种产品所用的材料方面几乎没有灵活性。
结果是,MRP被迫在不断缩短的时间尺度上工作,对材料订单的频繁,突然和迫切需求。这反过来又推动了采购政策的削弱,包括在许多情况下从“灰色市场”购买材料。显然,非常强烈要求对这些MRP和ERP工具进行某种形式的增强或改变,以便他们能够克服这些挑战。
返回列表